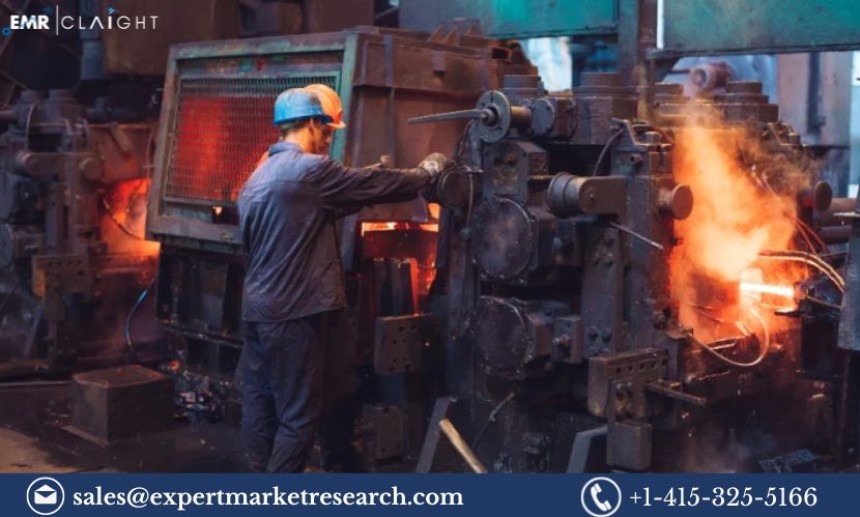
Sponge Iron Manufacturing Plant Project Report 2024: Processes, Costs, and Considerations
Explore our comprehensive report on setting up a Sponge Iron Manufacturing Plant, covering production, market demand, and investment insights.
2024-12-16 08:53:06 - Lewis Fernandas
Introduction
A Sponge Iron Manufacturing Plant Project Report is a vital resource for businesses looking to establish a production facility for sponge iron, also known as direct reduced iron (DRI). Sponge iron is a crucial component in the steel manufacturing process, used as a substitute for scrap metal in electric arc furnaces and in the production of high-quality steel. As global demand for steel continues to rise due to infrastructure development, urbanization, and industrialization, establishing a sponge iron manufacturing plant has become a profitable venture. This article explores the key aspects of setting up a sponge iron manufacturing plant, including the production process, required equipment, market dynamics, and financial considerations.
What is Sponge Iron?
Sponge iron is a form of iron that is produced through the reduction of iron ore (usually iron oxide) in the presence of a reducing agent, such as natural gas or coal. Unlike blast furnace iron, sponge iron is produced in a more environmentally friendly process and is considered a more sustainable option. Sponge iron is called "sponge" because of its porous nature, which allows it to be easily melted down and used in steel production.
There are two main types of sponge iron production methods:
- Direct Reduction (DRI): This method involves the reduction of iron ore to iron using a reducing gas, typically produced from natural gas, and producing sponge iron in the form of small, round pellets or lumps.
- Indirect Reduction (or Coal-Based Reduction): In this method, iron ore is reduced using coal in a rotary kiln to produce sponge iron.
Market Demand for Sponge Iron
The market for sponge iron has grown significantly over the past few decades due to several factors:
- Rising Demand for Steel: The global steel industry is expanding rapidly, especially in developing economies. Steel is essential for the construction of infrastructure, automobiles, and machinery, leading to increased demand for iron and steel production materials, including sponge iron.
- Preference for Eco-friendly Steel Production: Sponge iron production is seen as a more environmentally sustainable alternative to traditional blast furnace iron. This is because the production process emits fewer pollutants and carbon dioxide compared to traditional iron-making methods, making it increasingly attractive in the context of rising environmental awareness and stricter regulations.
- Growing Scrap Metal Shortage: The scarcity of scrap metal, particularly in regions where scrap metal is not abundant, has led steel manufacturers to rely more on sponge iron as a substitute material.
- Development of Steelmaking Technologies: Innovations in electric arc furnace (EAF) technology, where sponge iron is used as the primary feedstock, have also driven the demand for sponge iron. EAFs offer a more energy-efficient way to produce steel compared to traditional blast furnaces.
Production Process of Sponge Iron
The process of manufacturing sponge iron involves several stages, from the reduction of iron ore to the production of usable sponge iron, which is then supplied to steel mills and other industries. Below is a simplified overview of the sponge iron production process:
1. Iron Ore Mining and Preparation
The first step in the production of sponge iron is the procurement of iron ore, which is typically obtained from mines. The ore is then processed to remove impurities and prepared in the form of pellets or lumps. The iron ore must be of a specific grade and size to be suitable for reduction.
Get a Free Sample Report with Table of Contents@
2. Reduction Process
The reduction of iron ore is the core step in sponge iron production. This can be done using two main methods:
- Gas-based Direct Reduction (DRI): In this method, iron ore pellets or lumps are heated in a furnace, and a reducing gas, often produced by the reforming of natural gas, is passed through the ore. The gas reacts with the iron ore, removing oxygen and leaving behind iron in the form of sponge iron.
- Coal-based Reduction: In this process, iron ore is reduced in a rotary kiln using coal as the reducing agent. The coal reacts with the oxygen in the ore, producing iron and carbon dioxide. This method is more commonly used in areas with abundant coal resources.
The reaction results in sponge iron, which has a high iron content and is porous, making it ideal for use in steel manufacturing.
3. Cooling and Screening
Once the sponge iron has been produced, it is cooled and then screened to remove any unwanted material. The cooled sponge iron is then graded according to its size and quality.
4. Quality Control and Testing
Sponge iron is subject to stringent quality control measures to ensure that it meets industry standards. This includes testing for the iron content, carbon levels, and overall purity. It is crucial that the sponge iron produced is of the highest quality to ensure it is suitable for use in steel manufacturing.
5. Packaging and Distribution
Finally, the sponge iron is packaged in appropriate containers for transport and distribution to steel plants and other industries. It may be delivered in bulk or in smaller quantities, depending on customer requirements.
Key Equipment for Sponge Iron Manufacturing
Setting up a sponge iron manufacturing plant requires specific equipment to carry out the production process. Some of the key equipment used in sponge iron manufacturing includes:
- Rotary Kilns: These are used for the reduction of iron ore using coal or other reducing agents in the coal-based method. Rotary kilns provide the required temperature and environment for the reduction process.
- Gas Reforming Units: In gas-based reduction plants, natural gas is reformed to produce the reducing gas used in the process. These units are essential for the efficient production of sponge iron in gas-based plants.
- Furnaces: Furnaces are used for heating the iron ore and reducing it in the gas-based method. They provide the high temperatures required for the reduction reaction to occur.
- Cooling and Screening Systems: These systems are used to cool the sponge iron after it has been reduced and then to sort and grade it based on size and quality.
- Quality Control Labs: These laboratories are equipped with testing instruments such as spectrometers and chemical analyzers to ensure the sponge iron meets the required quality standards.
- Packaging Units: After the sponge iron is processed, it is packaged in appropriate containers for transportation and delivery to customers.
Regulatory Compliance and Safety Considerations
Setting up a sponge iron manufacturing plant requires adherence to various safety and regulatory standards. Some of the key regulations and safety considerations include:
- Environmental Compliance: The production of sponge iron can result in emissions such as carbon dioxide, particulate matter, and other pollutants. Manufacturers must comply with local environmental regulations and invest in technologies such as gas cleaning systems and dust collection units to minimize emissions.
- Safety Standards: The manufacturing process involves handling high temperatures, chemicals, and heavy machinery. Ensuring the safety of workers through the installation of safety equipment, proper training, and adherence to safety protocols is crucial.
- Quality Assurance: Compliance with industry standards for product quality is necessary for maintaining the credibility of the product. Regular quality checks and adherence to international standards ensure the sponge iron meets the requirements of steel mills and other industries.
- Health and Safety Compliance: Regular safety audits and the implementation of health and safety regulations are critical to prevent accidents and maintain worker safety. Proper ventilation, protective gear, and emergency protocols must be in place to safeguard workers.
Financial Considerations and Investment
Setting up a sponge iron manufacturing plant requires significant investment, and it is crucial to assess the financial viability of the project. Some of the key financial aspects to consider include:
- Initial Capital Investment: The cost of land, building infrastructure, purchasing equipment, and obtaining licenses for regulatory compliance can be substantial. A well-detailed business plan is necessary to estimate the total capital required.
- Operational Costs: Operational expenses include raw material procurement (iron ore, coal, natural gas), labor, utilities (electricity, water), and maintenance of machinery. The cost of raw materials will vary depending on the quality of iron ore and coal used in the production process.
- Revenue Generation: The revenue potential of the sponge iron manufacturing plant will depend on the production scale, pricing strategy, and the demand for sponge iron in the steel industry. Establishing strong partnerships with steel manufacturers and other industrial clients can contribute to stable revenue streams.
- Return on Investment (ROI): The ROI for a sponge iron manufacturing plant will depend on production efficiency, market demand, and operational cost management. It is important to create a detailed financial model to estimate profits over time.
FAQs1. What is sponge iron used for?
Sponge iron is primarily used in steel manufacturing. It serves as a feedstock in electric arc furnaces, replacing scrap metal, and helps in producing high-quality steel.
2. What are the main methods for producing sponge iron?
Sponge iron is produced through two main methods: gas-based direct reduction (using natural gas) and coal-based reduction (using coal as the reducing agent).
3. What raw materials are required for sponge iron production?
The primary raw materials include iron ore, coal (or natural gas for the gas-based process), and other auxiliary materials needed for the reduction process.
4. What are the environmental concerns in sponge iron manufacturing?
Sponge iron manufacturing can produce emissions such as carbon dioxide and particulate matter. Compliance with environmental standards and the installation of gas cleaning and dust control systems is crucial to minimize the environmental impact.
5. How does the demand for sponge iron affect the industry?
The increasing demand for steel, along with the preference for sustainable manufacturing processes, has driven the demand for sponge iron, making it a key product in the global steel industry
Media Contact:
Company Name: Claight Corporation
Contact Person: Lewis Fernandas, Corporate Sales Specialist — U.S.A.
Email: sales@expertmarketresearch.com
Toll Free Number: +1–415–325–5166 | +44–702–402–5790
Address: 30 North Gould Street, Sheridan, WY 82801, USA