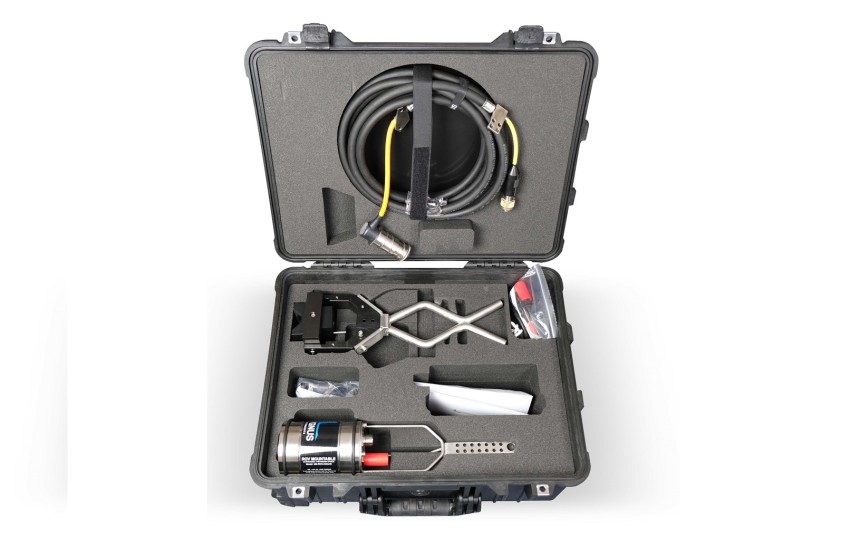
Applications of Ultrasonic Thickness Gauges
Explore diverse applications of ultrasonic thickness gauges in industries like oil, aerospace, and construction. Learn how UTM ensures safety and efficiency.
2024-12-05 12:02:56 - James Clark
Ultrasonic thickness gauges are indispensable tools in industries requiring precise material thickness measurements. These devices use high-frequency sound waves to detect corrosion, wear, and inconsistencies in various materials, ensuring safety and efficiency. If you're curious about UTM ultrasonic thickness measurement, learn more about advanced solutions.
What Are Ultrasonic Thickness Gauges?Ultrasonic thickness gauges (UTGs) are non-destructive testing tools that measure the thickness of a material by sending sound waves through it. The waves reflect off the back surface of the material, and the device calculates the thickness based on the time the sound takes to return.
Key Features of UTGs- Precision in detecting material thinning.
- Non-invasive, preserving material integrity.
- Usable on various materials, including metals, plastics, and composites.
UTGs help identify areas of wear and corrosion, preventing potential failures.
Improves SafetyBy detecting flaws early, these tools reduce risks to equipment, infrastructure, and human safety.
Cost-Effective MaintenanceEarly detection minimizes expensive repairs or replacements.
Applications Across Industries1. Oil and Gas IndustryPipeline MonitoringPipelines are exposed to corrosion due to harsh environmental conditions. UTGs monitor the thickness of pipeline walls, ensuring they meet safety standards and preventing leaks.
Storage Tank InspectionIn refineries, storage tanks hold hazardous materials. UTGs help detect thinning tank walls, preventing potential spills or accidents.
2. Marine and ShipbuildingHull Integrity ChecksShip hulls constantly face exposure to water, leading to corrosion. UTGs monitor hull thickness, ensuring vessels remain seaworthy.
Offshore PlatformsUTGs are used to inspect structural components of offshore rigs, ensuring stability in challenging conditions.
3. Aerospace IndustryAircraft Component TestingUTGs inspect critical aircraft components like wings and fuselages, ensuring they meet stringent safety regulations.
Detection of Hidden CorrosionAerospace materials often face internal corrosion. UTGs can detect flaws that are invisible to the naked eye.
4. Manufacturing and Industrial PlantsQuality ControlUTGs ensure materials meet specified thickness requirements, maintaining production quality.
Equipment MaintenanceMachinery components can wear out over time. UTGs monitor wear, enabling timely repairs and prolonging equipment life.
5. Construction IndustryStructural AssessmentsUTGs inspect beams, columns, and other structural elements to ensure they meet safety codes and are free from defects.
Bridge InspectionsBridges endure constant stress and environmental exposure. UTGs help identify weak points in the structure.
6. Power GenerationBoiler InspectionsPower plants rely on boilers that face extreme heat and pressure. UTGs detect thinning walls, preventing catastrophic failures.
Turbine MonitoringTurbine blades must withstand high stress. UTGs ensure they remain in optimal condition.
7. Automotive IndustryChassis InspectionsUTGs check for material uniformity in vehicle frames, ensuring durability and crash safety.
Component TestingParts like fuel tanks and exhaust systems are tested for wear and corrosion.
8. Food and Beverage IndustryEquipment MaintenanceProcessing equipment like tanks and pipes are monitored for wear to maintain hygiene and efficiency.
Regulatory ComplianceUTGs ensure that equipment complies with health and safety regulations.
Advantages of Using Ultrasonic Thickness GaugesHigh AccuracyUTGs deliver precise measurements, even for thin or complex materials.
Non-DestructiveTesting does not damage the material, preserving its integrity.
Real-Time ResultsUTGs provide instant feedback, enabling quick decision-making.
VersatilityApplicable across various industries and materials, UTGs offer unmatched flexibility.
How to Use Ultrasonic Thickness Gauges EffectivelyStep 1: Surface PreparationClean the material surface to remove dirt, rust, or coatings that might interfere with the sound waves.
Step 2: Couplant ApplicationApply a couplant gel to eliminate air gaps and ensure efficient sound wave transmission.
Step 3: CalibrationCalibrate the UTG to match the material's properties for accurate readings.
Step 4: TestingPlace the transducer on the material and record the thickness readings displayed on the device.
Choosing the Right Ultrasonic Thickness GaugeMaterial CompatibilitySelect a gauge that works with the materials you’ll be testing.
Operating EnvironmentEnsure the gauge can withstand the conditions it will be used in, such as extreme temperatures or underwater.
PortabilityFor fieldwork, choose a lightweight and portable UTG.
Advanced FeaturesModern UTGs come with features like data storage, wireless connectivity, and automated reporting.
Limitations of Ultrasonic Thickness GaugesWhile UTGs offer numerous benefits, there are some limitations:
- Requires proper surface preparation for accurate results.
- Limited by the skill and experience of the operator.
- May struggle with highly irregular or complex surfaces.
AI-powered UTGs can provide predictive analytics, improving maintenance planning.
Robotics and AutomationDrones and robots equipped with UTGs can access hard-to-reach areas, enhancing efficiency.
MiniaturizationCompact UTGs with advanced features are becoming increasingly available, making them ideal for more applications.
ConclusionUltrasonic thickness gauges are crucial tools for ensuring the safety, quality, and efficiency of materials and equipment across various industries. From oil pipelines and ship hulls to aircraft components and industrial machinery, UTGs play a vital role in maintaining operational standards and preventing costly failures.